【SPECIAL EDITION】 In-depth Explanation of Positioning Touch Switch Selection and Terminology
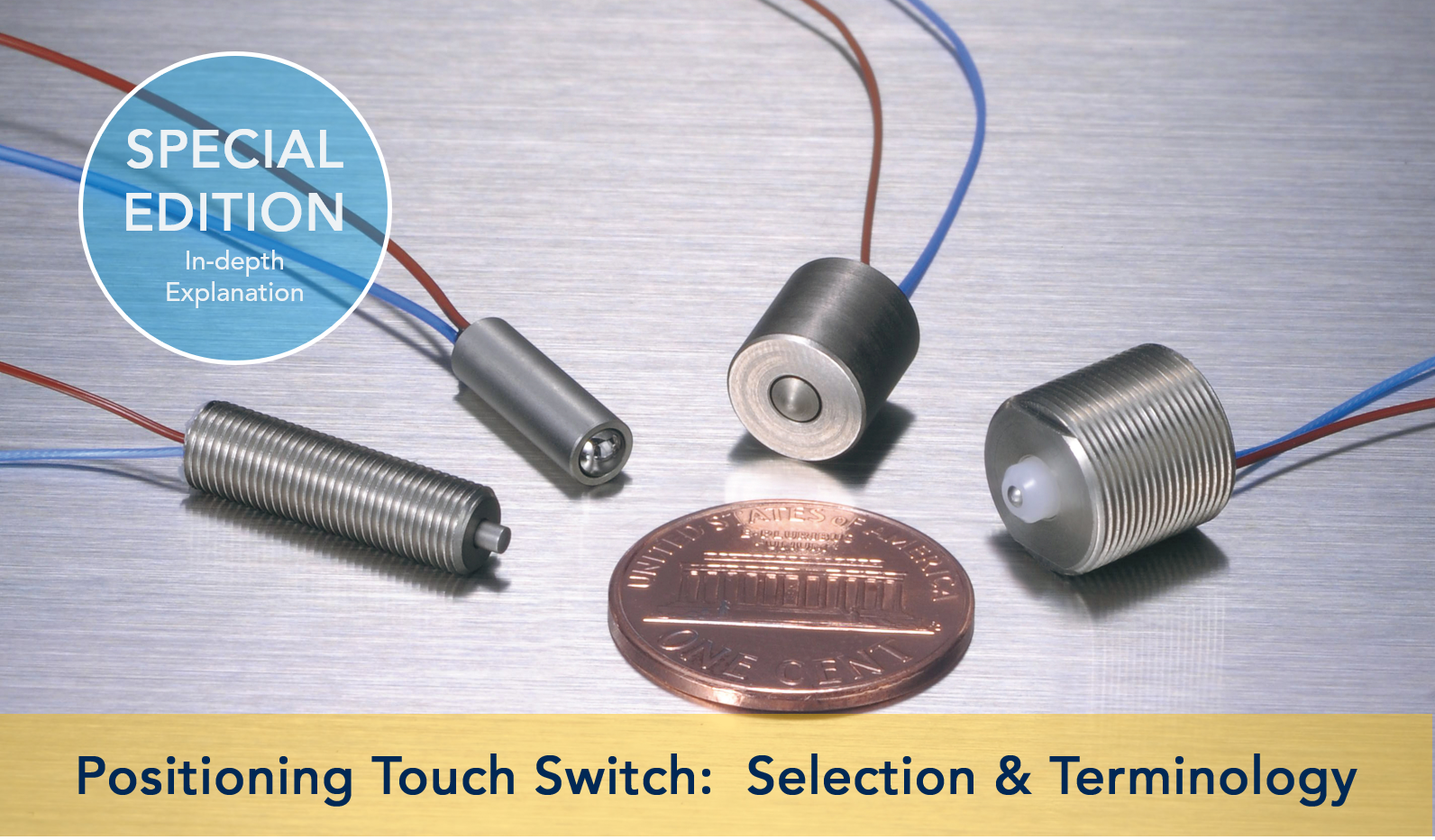
Table of Contents
What is a Positioning Touch Switch?
The "Positioning Touch Switch" is a contact-type sensor that outputs an ON/OFF signal by touching the sensing object.
Its main applications are to confirm the seating and positioning of the sensing workpiece. Although similar to limit switches and micro-switches in application, they differ greatly in terms of accuracy and durability. That is why touch switches can be installed not only on robots but also in adverse environments such as machine tools.
They serve to accurately determine the position of tools and workpieces, enabling high-precision machining and reduction of defective products.
The method of operation, the position to be operated, the motion of operation, and the force required for operation differ depending on the type of switch.
This article describes the basic structure and terminology useful for selecting touch switches.
【 Demonstration Video 】Application Examples of Positioning Touch Switches
First, please watch the video (3 min. 20 sec.) of an application example of positioning touch switches.
The video introduces a "workpiece transfer robot" incorporating a positioning touch switch.
The “Workpiece Transfer Robot” uses switches to perform the following operations:
・Clamping the workpiece and confirming that it is seated.
・Positioning of jig
・Checking the position of the table
Specifications of Touch Switches
Operating Forms (NO and NC)
There are two types of signal formats output from the contact:
Normally open (NO) and Normally closed (NC)
《 Normally Open 》
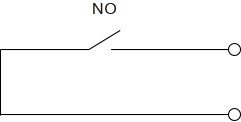
《 Normally Closed 》
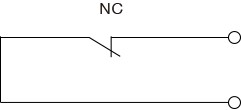
Bearings (metal and ball bearings)
There are two types of bearings: Metal and Ball bearings.
The type of bearing you may select depends on the way the contact-point is applied to the workpiece.
《For straight-on touch application》
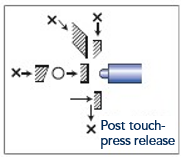
If the sensing workpiece can be pushed straight-on, you can choose either metal or ball bearing bearings.
《For angled-touch application》
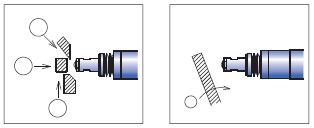
If the axis is subjected to tilt when the contacts are pushed against it, then select "ball bearings".
What is a Contact (Ball and Flat type)
The "contact" is the part at the tip of the switch that touches the sensing workpiece.
It is also called a "contact probe".
When the contact-probes are pushed in and the internal contacts touch each other or separate, current is energized and a signal is output.
The contact shape can be roughly selected from "ball" and "flat".
Selecting the appropriate one for the shape of workpiece will stabilize the accuracy.
● Ball type:
Select "Ball type" contacts if the object has a flat shape.
● Flat type:
When the object is spherical, convex or curved, please select "flat" type contacts.
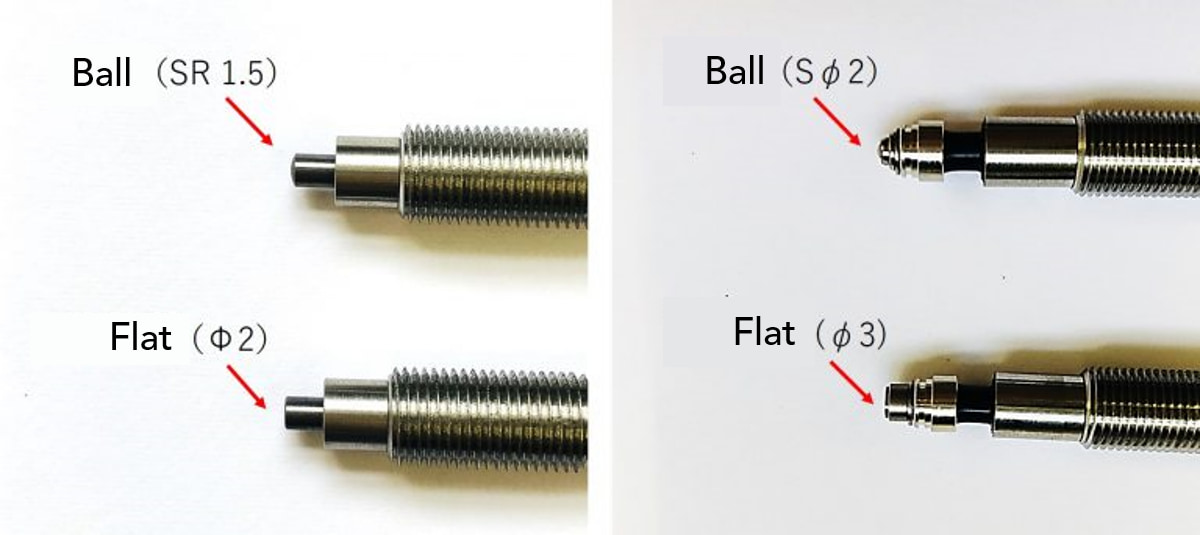
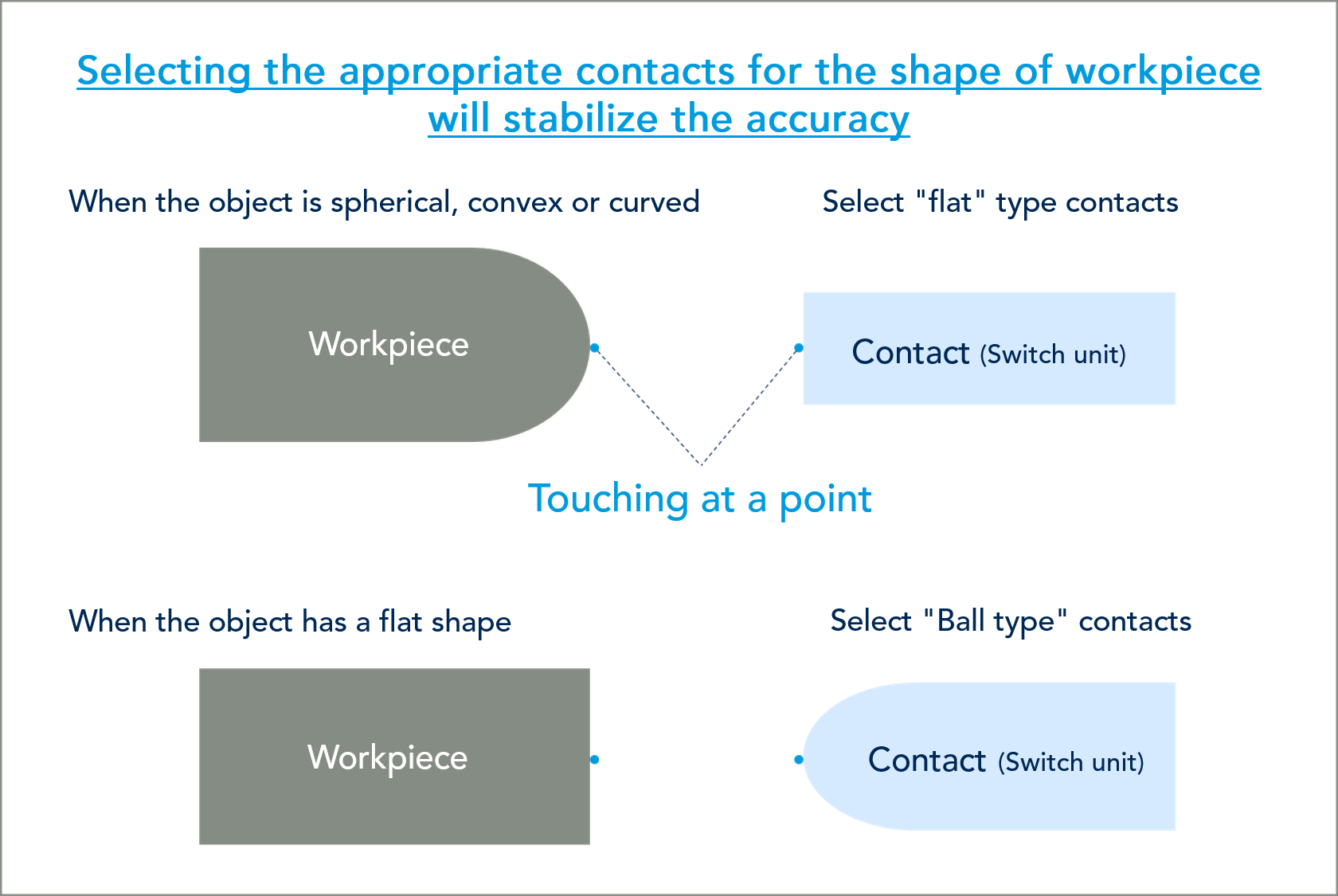
What is Waterproof Construction (IP Protection Rating)?
“IP protection rating” refers to the level of dustproof and waterproof.
Many of METROL's sensors, including high-precision touch switches, have a high waterproof rating of IP67. Therefore, our sensors can be used in adverse environments with coolants and chips splashed on the machine tools.
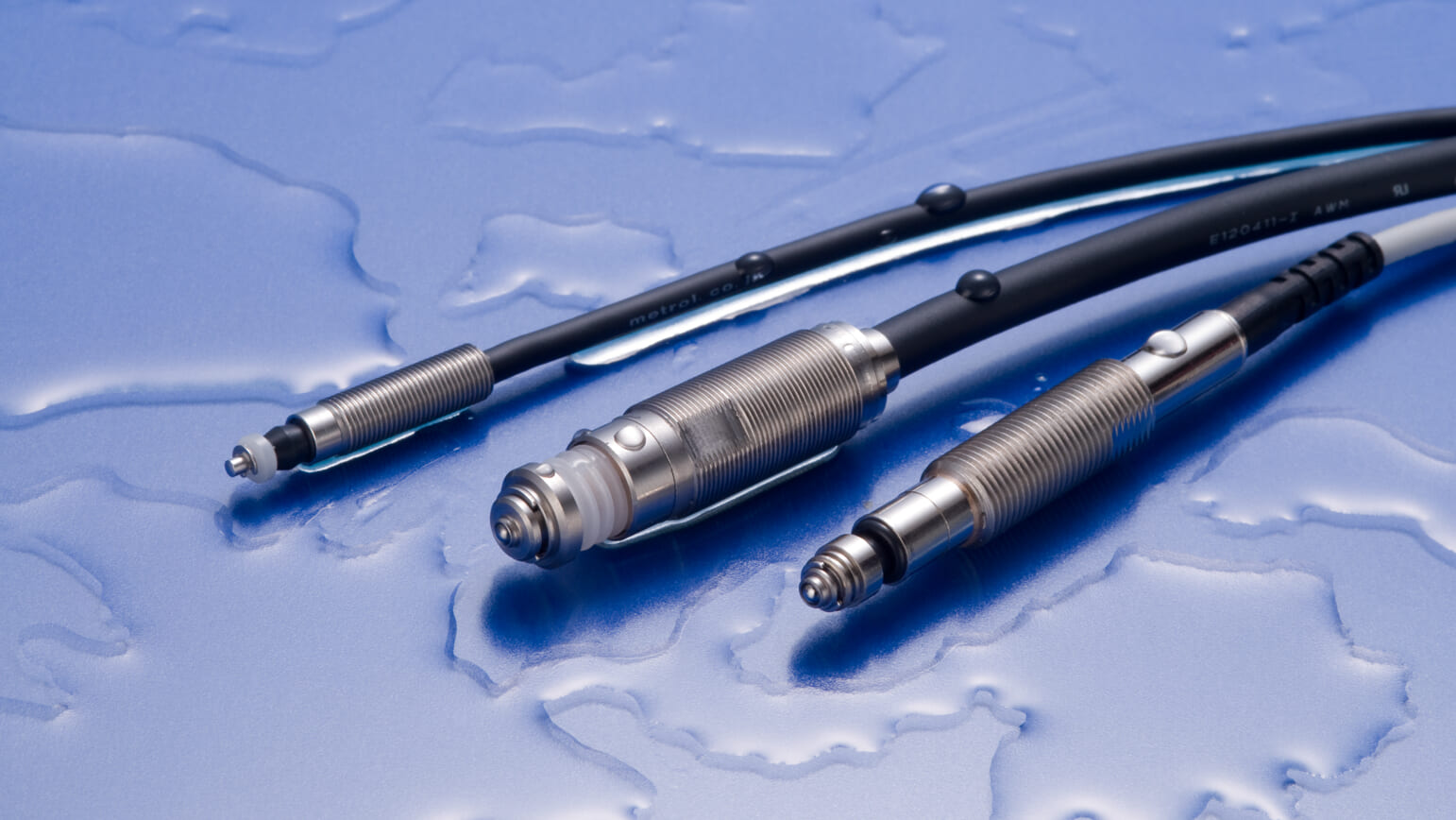
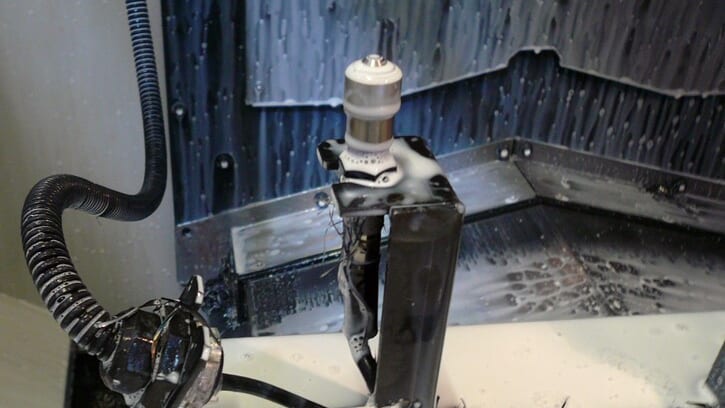
[Glossary] Touch Switch Term
In selecting a positioning touch switch, you should consider the following questions
- How long do I have to push the contact in before it operates?
- When does the signal switch over (return)?
- How much load must be applied?
The following is a list of terms that are necessary for selection.
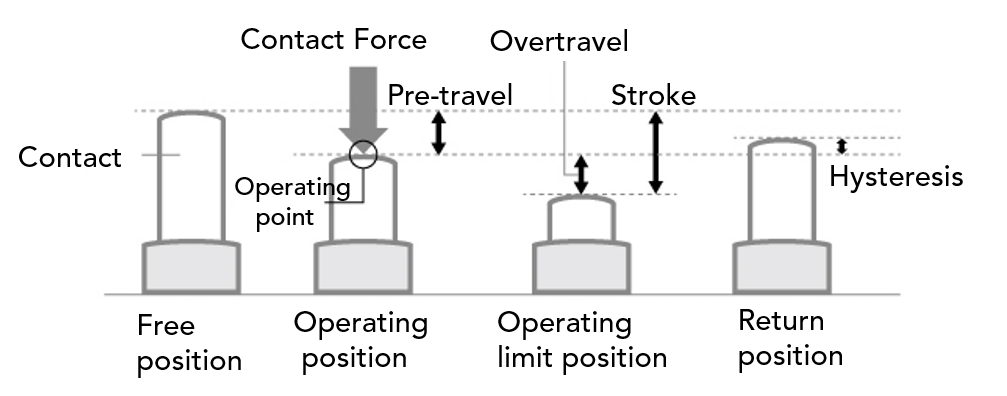
|
Term
|
Unit
|
Definition
|
Position
|
Free position |
mm |
The position of a contact when no force is applied to it |
Operating position | mm | The position where the signal switches when the contact-probe is pushed in | |
Return position | mm | The position where the switched signal returns | |
Operating limit position | mm | The position when the contact-probe is pushed all the way out | |
Operation
|
Stroke |
mm |
Overall movement |
Pre-travel(PT) | mm |
Movement up to the point of operation |
|
Overtravel(OT) | mm |
The amount of movement that can be pushed in after the signal is switched. Stroke minus pre-travel |
|
Force
|
Contact force | N |
Force required to switch the signal |
Return force | N |
Force required to move the signal from the operating limit position to the return position (spring force) |
|
Precision
|
Repeatability | mm |
Difference in positional variation of the signal operating point |
Hysteresis | mm | The difference in distance from the point of sensor operation to the point of signal return | |
Temperature drift | mm |
The range of variation of the signal operating point due to changes in environmental temperature |
[TERMINOLOGY] Structure of Positioning Touch Switches
Position at Which The Signal Switches
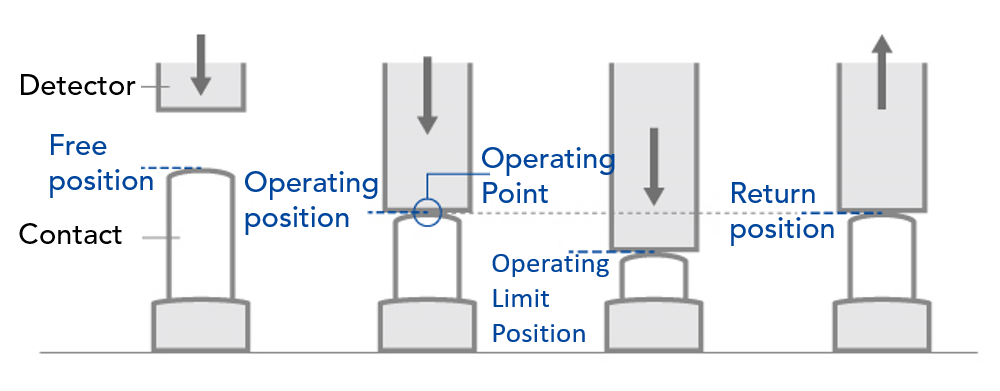
● Free position
The position of the contact when nothing is touching the contact-probe.
● Operating position
The position where the signal switches when the contact is pushed in.
● Operation Limit Position
The position where the contact is fully pushed in and cannot be pushed in any further.
●Return position
The point at which the switched signal returns, i.e., from the operating position to the free position.
For METROL's sensors, the operating position = return position, and there is no hysteresis.
Operation of Touch Switches
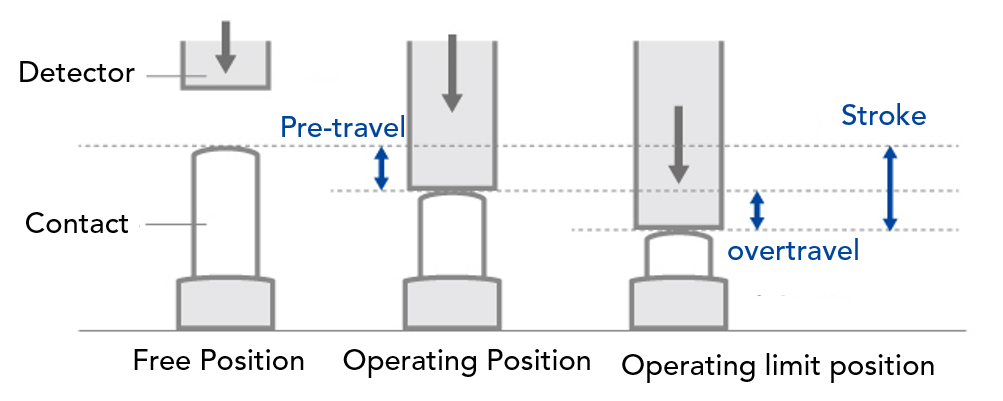
● Stroke
Stroke refers to the "overall movement".
It is the maximum amount (mm) that can be pushed into a contact, and is the distance traveled from the free position to the operation limit position.
● Pre-travel
Pre-travel is the amount by which the contact is pushed in before the signal is switched.
This is the distance from the free position to the operating point, also known as slack.
Normally open (NO) type always has pre-travel.
Normally closed (NC) types are available with or without pre-travel.
With pre-travel, the full pre-travel distance must be pushed in until the signal is switched.
It prevents false reactions due to vibration, shock, or the use of heavy contacts.
On the other hand, without pre-travel, the signal switches immediately when the contact is pushed in.
Since the amount of push-in is minimal, the force load on the sensing object can be reduced.
● Overtravel
This is the amount of further push-in from the point where the signal switches.
It is the distance from the stroke minus the pre-travel.
The larger the overtravel, the more likely it is that the sensing object will not break the sensor.
Some sensors are equipped with an "overtravel signal".
An "overtravel signal" is a signal to prevent the contact from being pushed in too far.
Force that Operates the Touch Switch
● Contact force
This is the force required to push the contact to the position where the signal is switched (unit: N).
The contact force increases according to the amount of contact push-in.
When using a heavy contact, please pay attention to the following points.
・When vertical mounting is used horizontally:
The contact force is increased by the weight of the movable part.
・When a horizontal mounting is used vertically:
The contact force is reduced by the weight of the movable part. Please be careful of return failure.
● Return Force
This is the force required to move the switch from the operation limit position to the return position.
In the case of our positioning touch switches, no force needs to be applied because the switch returns by the force of the internal spring.
[Terminology Explained] Precision of Touch Switches
Repeatability
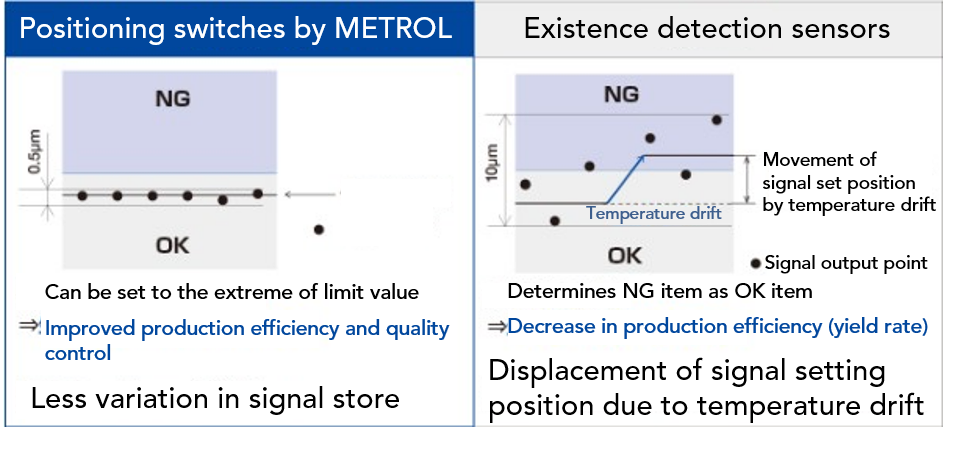
The difference in the variation of the signal operating point.
The difference between the maximum and minimum values is indicated by a range (R) based on the variation of the operating position when the sensing workpiece is placed perpendicular to the contact and pressed 30 times consecutively. (Our definition)
METROL's positioning touch switches have high repeatability and small signal operating point variation, enabling OK/NG recognition of objects with narrow tolerances.
Difference/Hysteresis
The difference in distance between the operating position and the return position.
METROL's contact-type sensors have no hysteresis.
In other words, the movement position and the return position are equal. The lack of hysteresis enables detection of fine motion of the workpiece.
On the other hand, electrical sensors (limit switches, microswitches, proximity sensors, optical sensors, etc.) are subject to differences. The inside of the hysteresis zone is a dead zone and cannot be detected, making it unsuitable for detecting minute movements of the workpiece.
Displacement between the operating position and the return position may be caused by deflection of the bracket (the pillar that holds the sensor in place) due to contact force, in addition to the switch itself.
For the type with large contact force, please pay attention to the rigidity of the bracket.
Temperature Drift
When the temperature of the sensor changes, the internal components expand and contract, causing a shift in the operating point.
METROL positioning touch switches themselves have no temperature drift.
Since it does not use electronic components, it has a simple structure with no heat source.
Sensors that use amplifiers will experience temperature drift.
Thank you for your attention to the above, an explanation of the basic structure of positioning touch switches and terminologies, which can be used when selecting sensors fit for your needs.