[Case Study] 3D Printer Modeling Accuracy Increased 10 Times by Using Touch Switches!
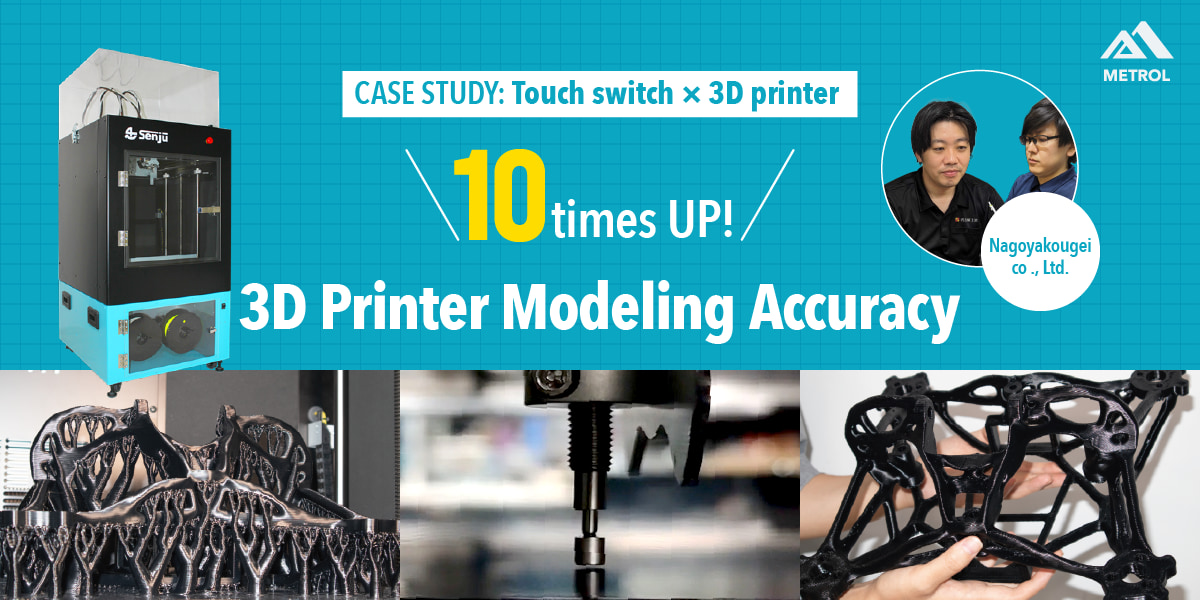
Table of Contents
Why do 3D printer molding defects occur?
Demand for 3D printers is growing.
In the manufacturing industry, it is now possible to create prototypes, custom parts, and other products with complex designs that were difficult to create using conventional manufacturing methods. Demand for 3D printers is expected to continue to grow as they are used in a variety of other industries, including medical, construction, aerospace, education, food, and fashion.
On the other hand, for those of you who are engaged in 3D printer production, do you have any of the following problems?
- Frequent modeling failures due to insufficient accuracy.
- Production time was wasted and deadlines were not met.
This article introduces the 3D printer manufacturer who realized high-precision modeling by installing METROL's touch switch on their 3D printer.
The surprising results are:
- Modeling accuracy increased by 10 times
- Modeling time 90% reduction in failure rate of the first layer
- Reproducibility increased 10 times UP!
Please read on!
what you learn form this article
- Why 3D printers produce molding defects
- How to use touch switches to improve molding defects
- How to use switches that are useful for designers
[Introduction of the interviewee] 3D printer manufacturer Nagoyakougei
This time we interviewed Nagoyakougei co ., Ltd.
This company manufactures 3D printers and operates a small-lot production business for industrial and consumer products using 3D printers.
They started development in 2023, saying, "If 3D printers on the market have so many problems, let's make our own ideal 3D printer.
The company is now attracting attention for its flagship product, 3D printer "Senju", the first commercial 3D printer in Japan equipped with an automatic nozzle tool changer.
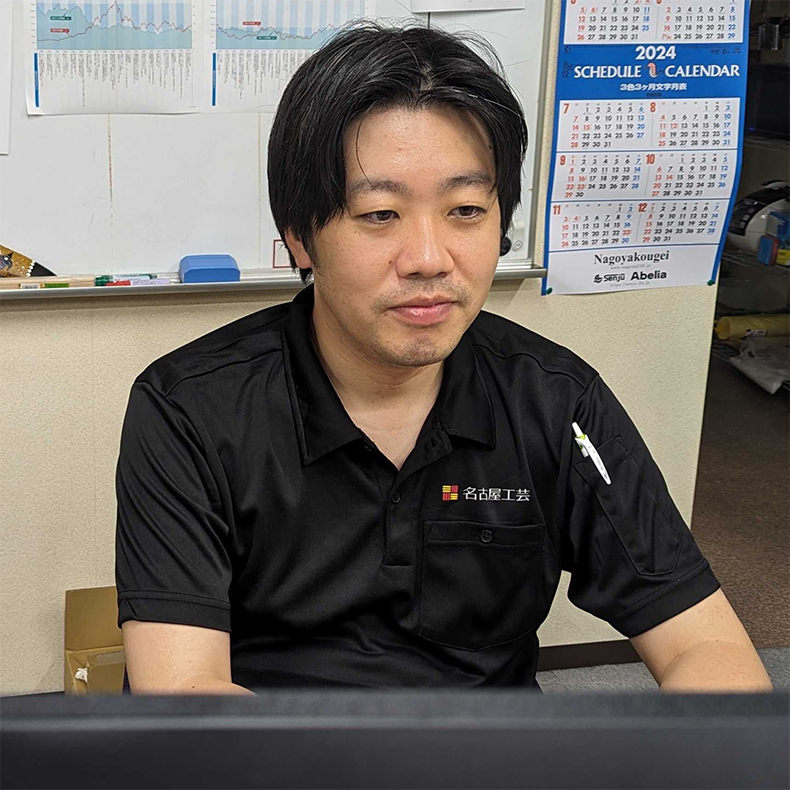
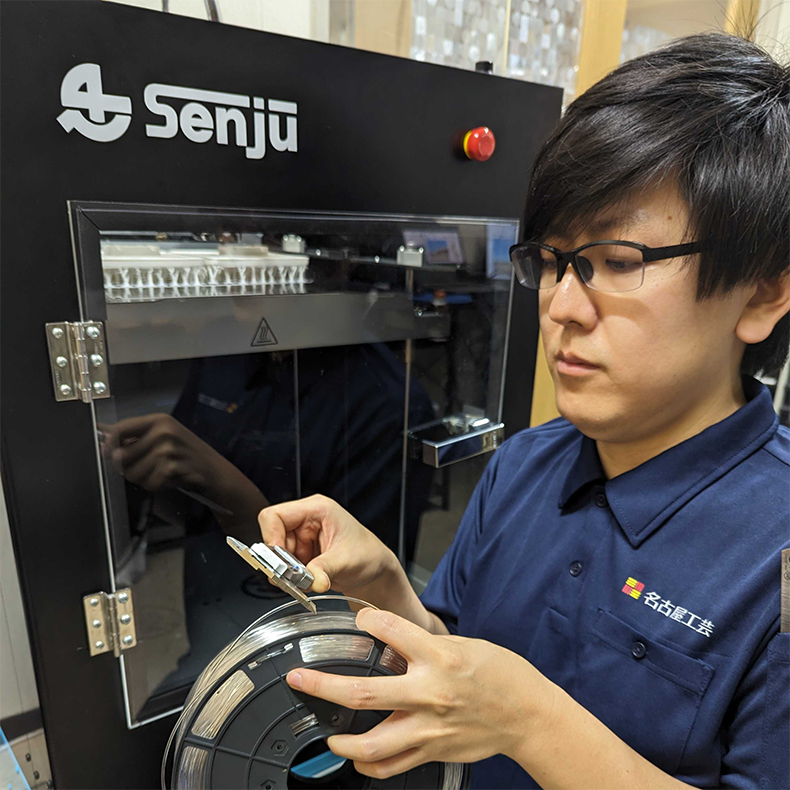
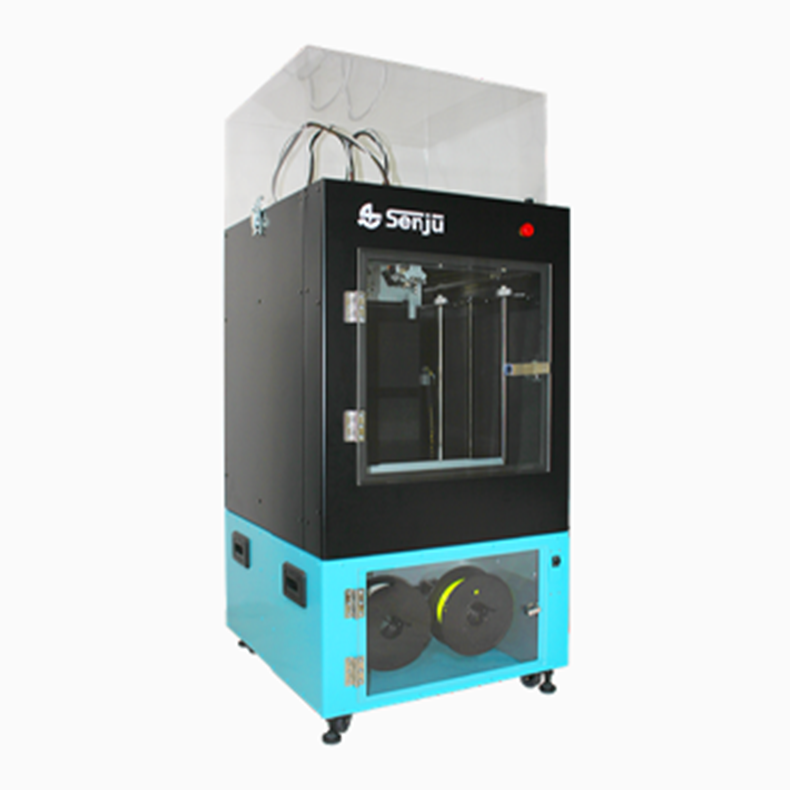
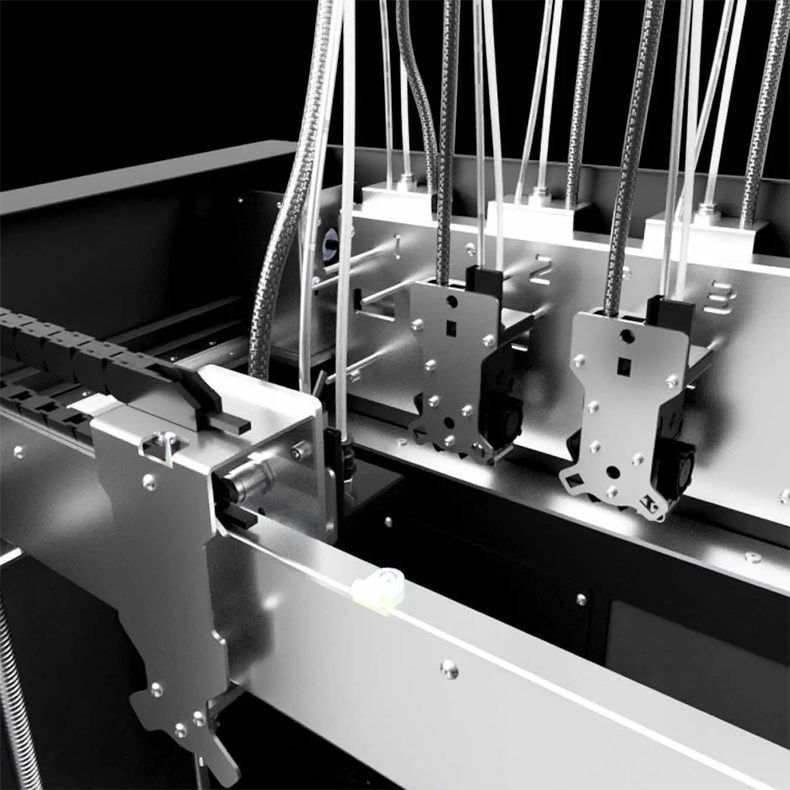
The most important issue in the development of the 3D printer
This paragraph will explain the challenges Nagoyakougei faced when developing its 3D printers and how it overcame them.
Issue: 90% of molding failures are caused by “poor molding of the first layer”.
Nagoyakougei believed that 90% of the defects in general 3D printers are caused by "first layer defects due to distortion of the production table".
Cause: Distortion of molding table that cannot be corrected
The following negative effects related to the molding table are the main reasons for defects in the first layer.
・Thermal expansion
・Scratches, stains, and bends on the table
・Accuracy of guides
Such table distortion is usually detected using "proximity sensors," but there have been many cases where the measurement accuracy was insufficient to avoid first-layer failure.
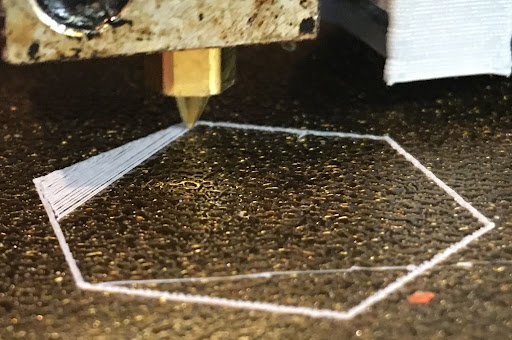
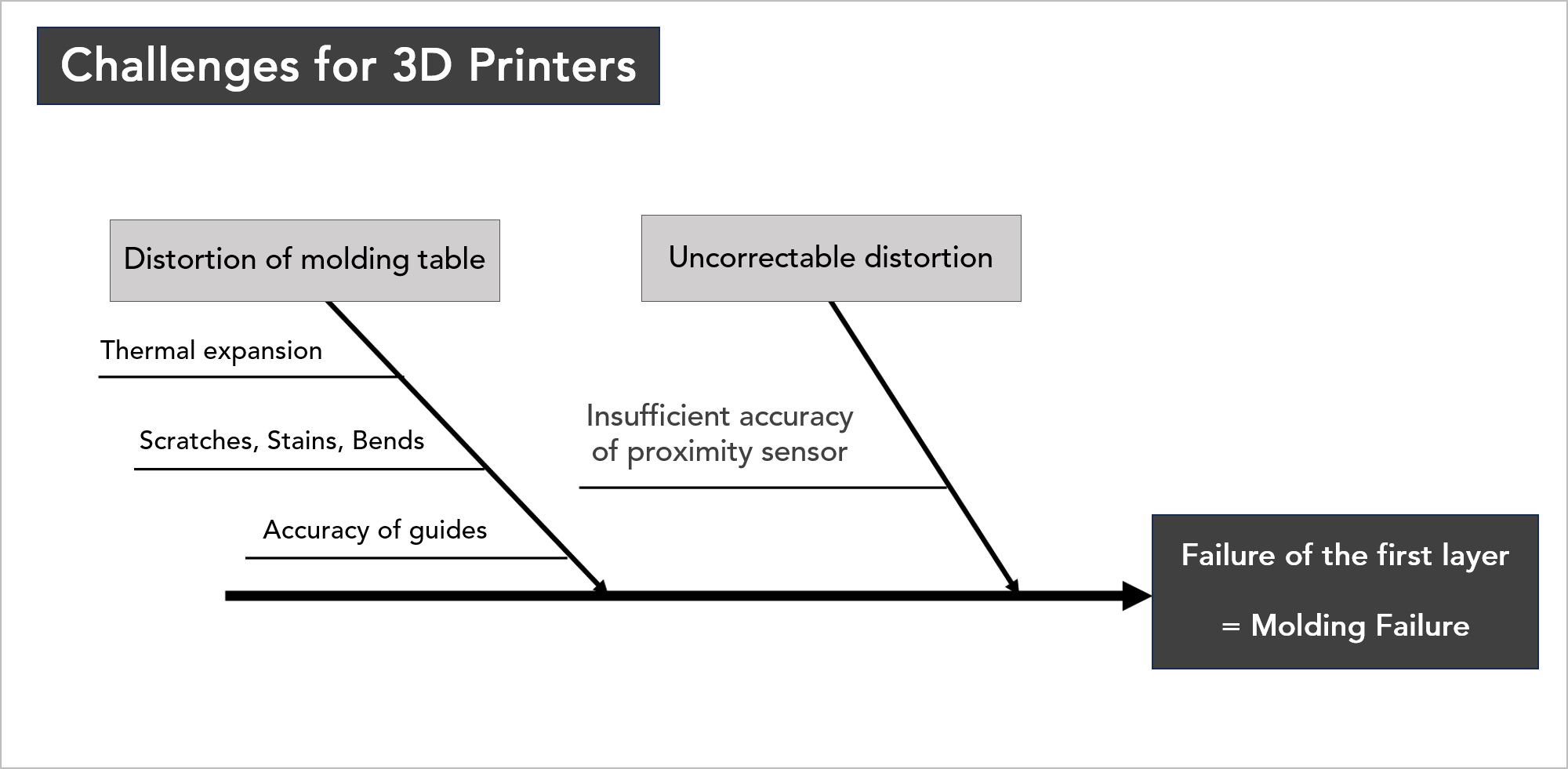
How have the 3D printer dramatically improved accuracy?
Nagoyakougei has developed a method to measure and correct molding table distortion, the key to molding accuracy, with extreme precision.
Solution: Utilize high-precision Touch Switches instead of proximity sensors
As a solution, "high-precision contact-type touch switches" were adopted in place of inaccurate proximity sensors.
By using a contact-type touch switch to precisely measure the distortion of the molding table, which could not be detected by the proximity sensor, they have succeeded in correcting the table distortion that causes molding failures in the first layer.
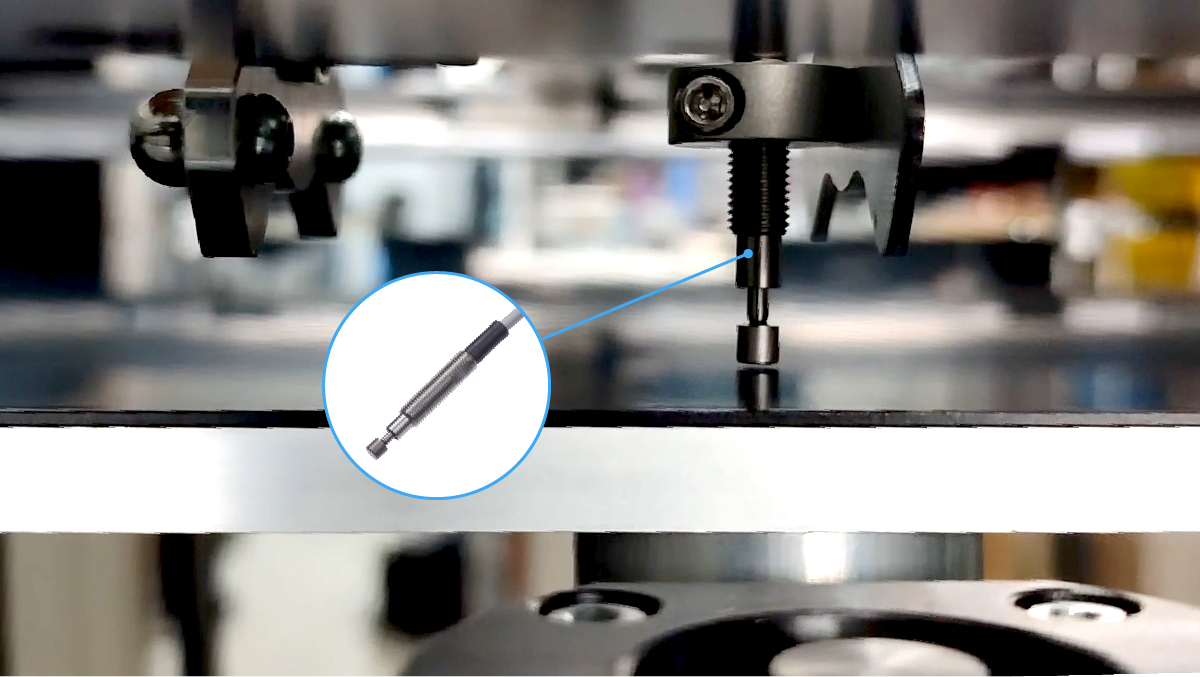
How to correct distortion by utilizing the Touch Switch
The process for correcting distortion of the modeling table using the touch switches is as follows:
1 . Measure the coordinates of multiple locations on the table with a touch switch
2 . Send measurement data to controller
3.Determine table distortion based on measurement data
4 . After measurement, the nozzle and touch switch are changed by automatic tool change, and molding begins while correcting the table height.
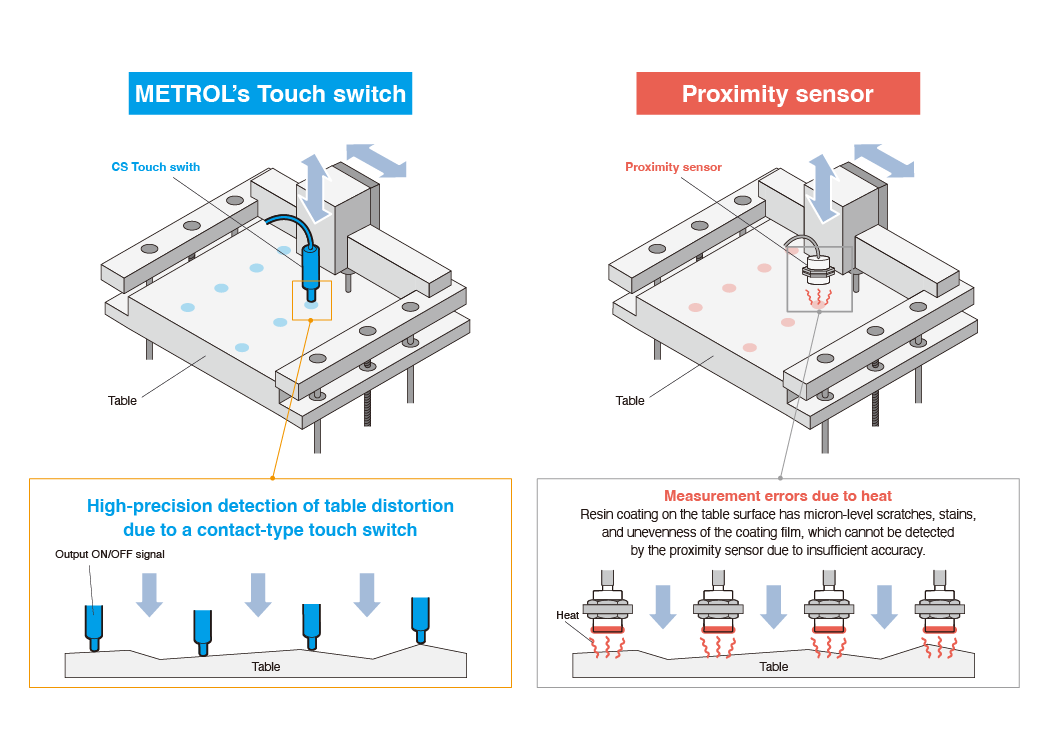
[Explanation Video] Method of measuring the molding table using a touch switch
Watch the video below to see how to actually measure the height of the modeling table using the touch switch.
By detecting multiple points on the table with touch switches, it is possible to determine the distortion of the entire table surface.
[Image] Firmware screen showing measured distortion of the molding table
The distortion of the modeling table measured by the touch switch is represented by a height map as shown below.
By correcting this distortion while molding the first layer, it is now possible to prevent "first-layer molding failures”.
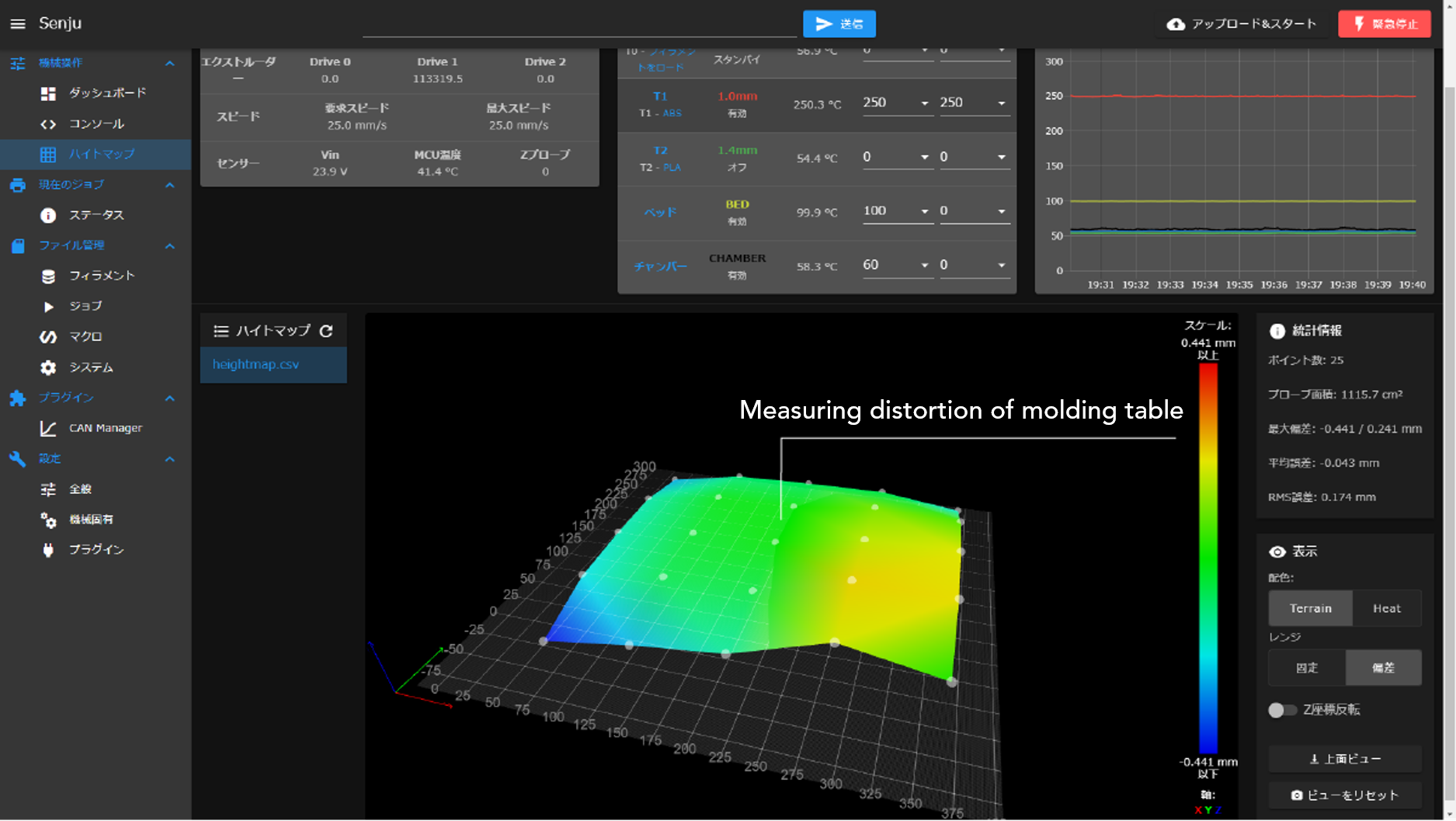
3 reasons why touch switches were chosen for 3D printers
Although similar products were on the shortlist, Nagoyakogei had no hesitation in choosing METROL products.
There are three reasons for this.
- METROL has an overwhelming track record of adoption in Japan and overseas, and has a strong brand name that can provide peace of mind.
- Cost-effective compared to expensive laser sensors, etc.
- After-sales service is reliable because of made in Japan
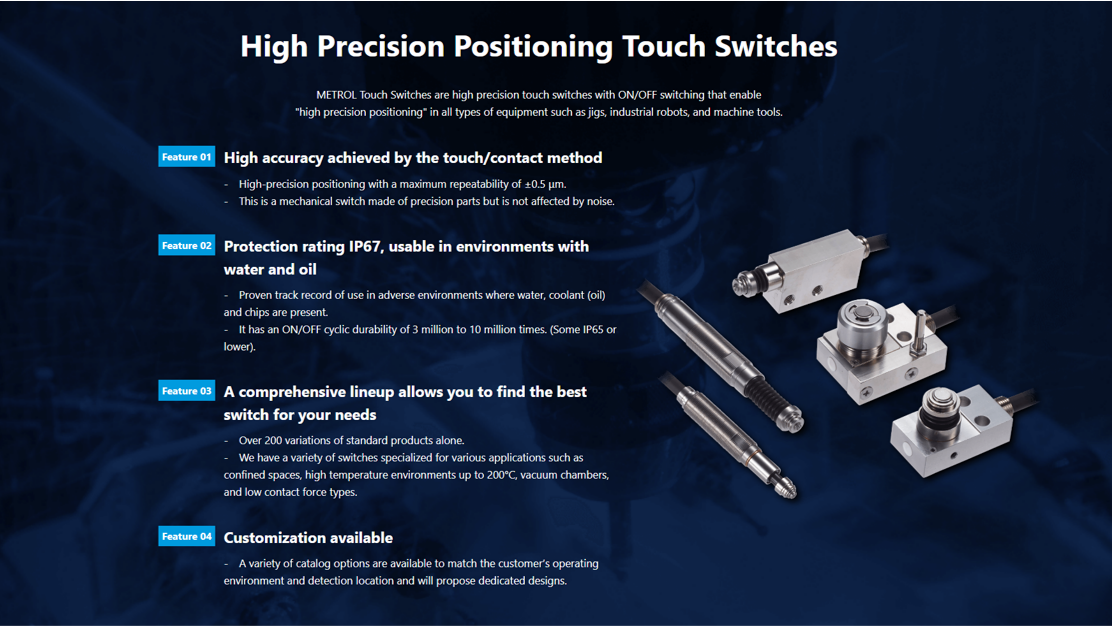
What are the results of Senju, a 3D printer equipped with touch switches?
The use of touch sensor has produced the following effects compared to conventionally used proximity sensors.
Results: Enabled measurement of molding table distortion with 10 times higher accuracy (50 μm → 5 um)
Generally, the specifications for sensors in the 3D printer market state 0.05mm (50μm), but Nagoyakogei's "Senju" can now measure with 10 times that accuracy. This repeated measurement enabled highly accurate modeling.
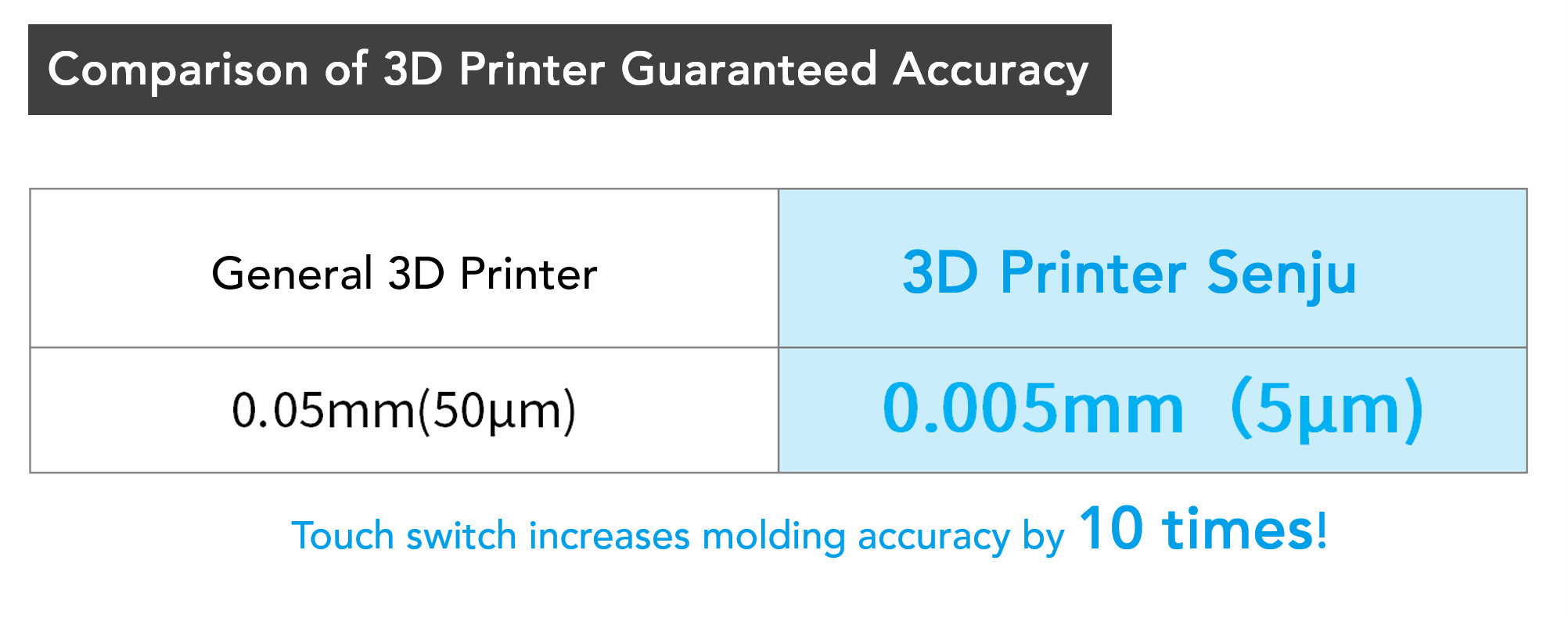
Greatly improved quality of moldings
High-precision modeling is made possible by controlling the distance between the modeling table and nozzle with the most precise values possible.
Senju is equipped with an automatic tool change function that automatically changes the nozzle.
The greatest advantage is that the nozzle diameter can be freely changed to increase the range of reproducibility of modeling and the speed of large-size modeling.
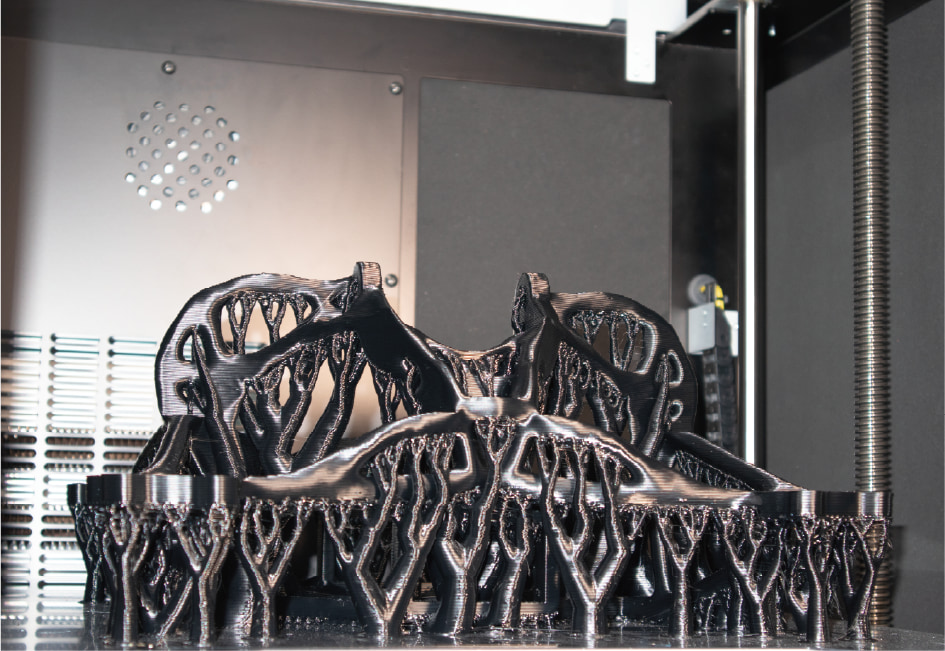
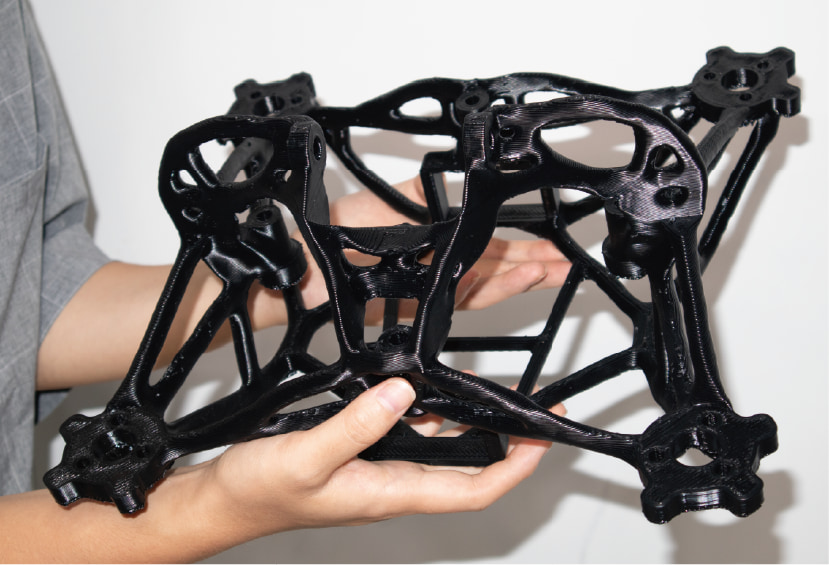
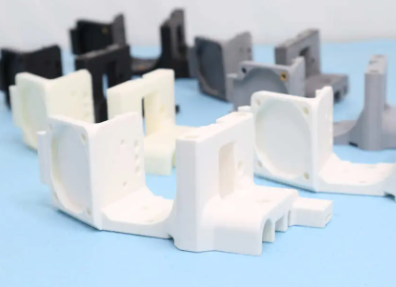
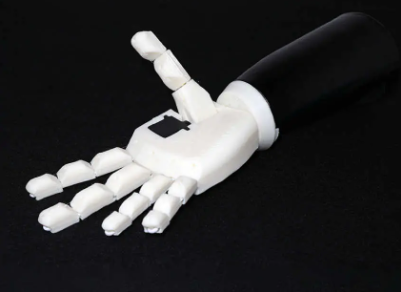
The failure rate of the first layer has been significantly reduced!
3D printer utilization rate and productivity have been improved.
The use of touch switches has resulted in the following effects.
- Significantly reduced failure rate in the first layer
- By utilizing touch switches, large-size modeling of more than 350mm2, which was previously possible only with expensive printers, is now possible at low cost and with high precision. The cost has been reduced to approximately half the level of conventional printers.
- Rapid molding is now possible. The number of setup operations, such as cleaning the production table and reheating the equipment, which takes about 10 to 20 minutes when starting over, is drastically reduced.
- The height adjustment of the nozzle and table, which used to be done once a week, is now done once every six months, enabling the creation of stable modeling objects.
Future Vision of 3D Printer Manufacturer Nagoyakougei
We want to build a “machine tool” that can be mass-produced, not a 3D printer that makes prototypes.
Q. What kind of vision do you have for the future development of 3D printers?
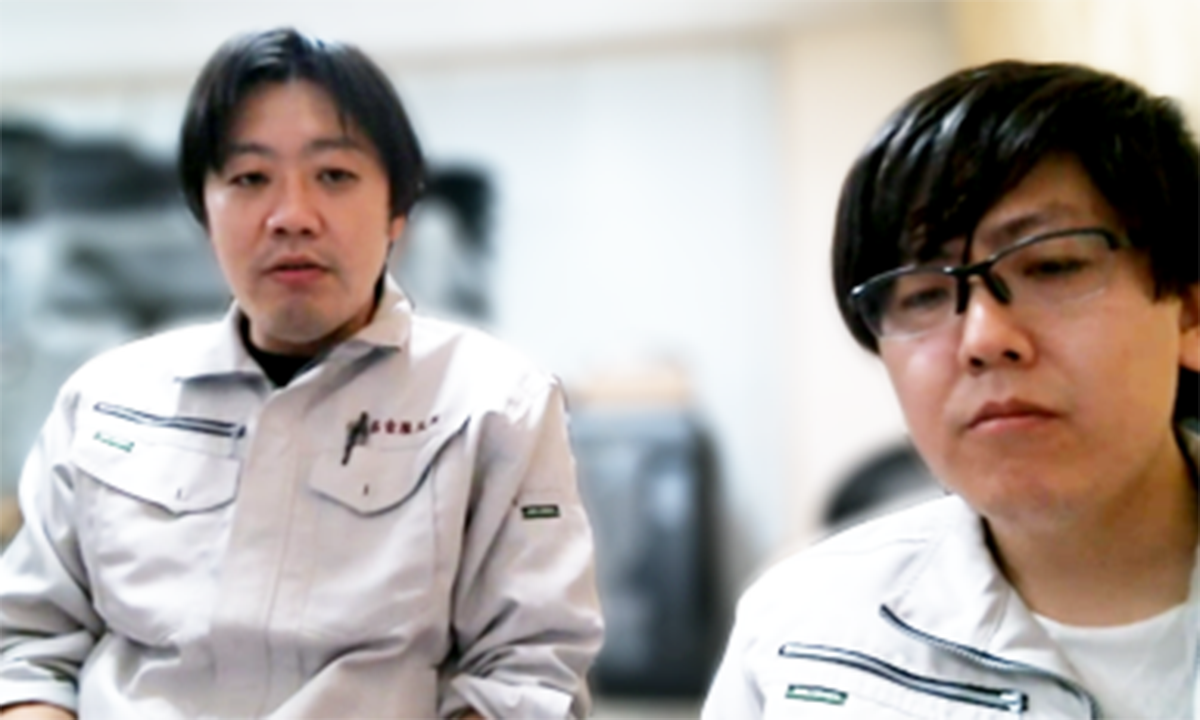
Nagoyakougei Technical Director, Wakimoto :
We would like to create a dream machine tool that is equipped with tools that can meet the needs of not only the manufacturing industry, but also the food, medical, agricultural, service, and many other industries. This is the concept behind the "Senju" concept, which means a thousand hands.
We are now approached by surprisingly large companies, and sometimes we have so many people coming to our factory that we can't fit them all in .
I can feel the strong interest in 3D printers in the society.
I want to contribute to the restoration of Japan as a technological superpower with Japanese-made 3D printers.
Nagoyakougei General Manager, Okada AM Division
Looking at the market, 3D printers are mostly foreign products.
There are currently only a few Japanese manufacturers' equipment that can be used with confidence, including support.
We began development with the desire to challenge this status.
If there is a Japanese-made 3D printer that can boost Japan's creative industry, Japanese manufacturing can retain more originality and advanced technology than ever before.
We will continue to strive for even higher performance and quality with the goal of contributing to Japan's manufacturing industry.
We hope that Metrol Sensors will be of service to Nagoya Kogei for your continued growth and development. Thank you very much.
Interview supported by Nagoyakougei co ., Ltd.
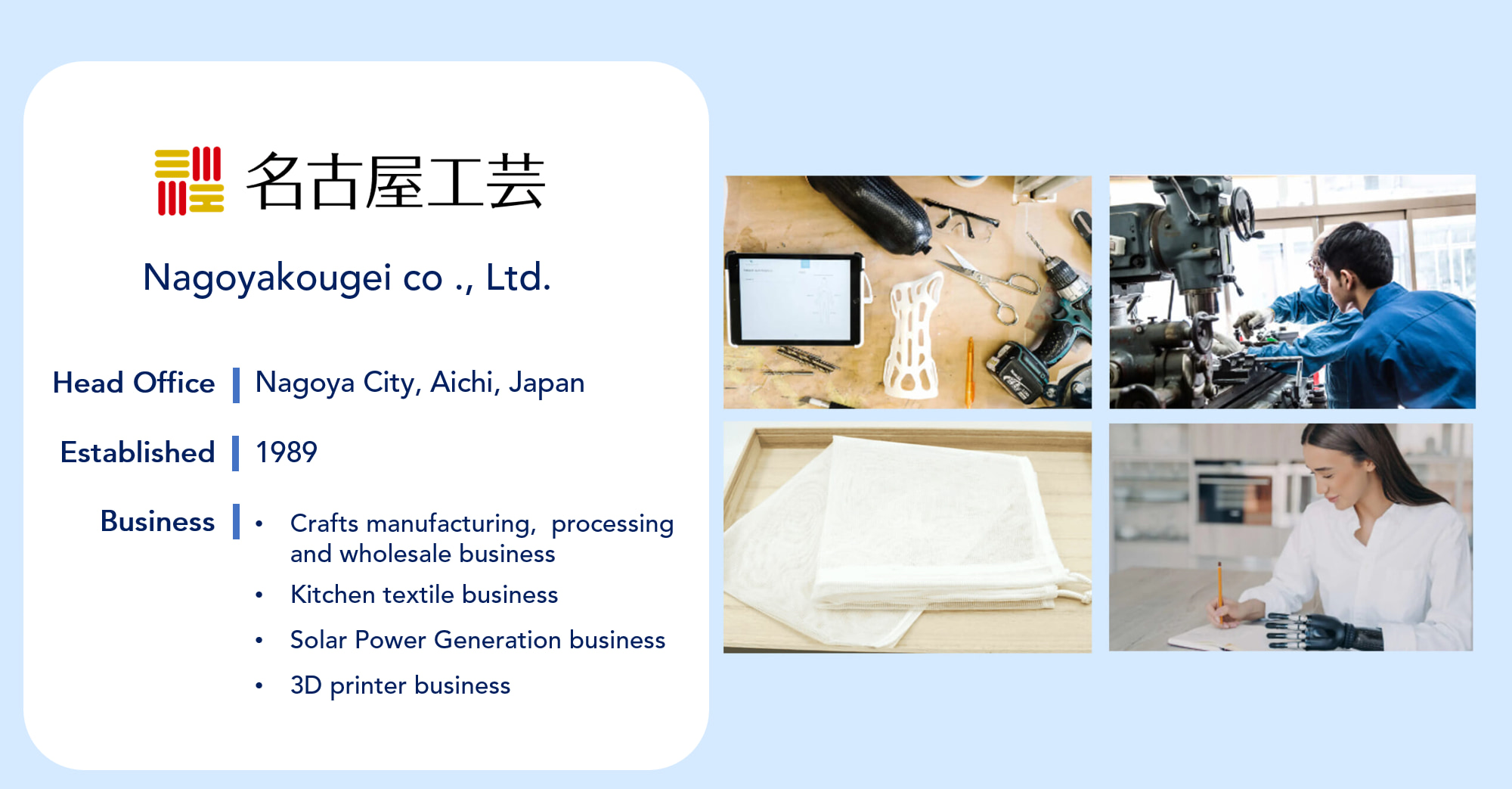
For product details
Compact, Low-cost CS series Touch Switches
Low-cost touch switch series.
Slim M5 to M10 design, 5μm repeatability, low cost.
A wide range of measuring element variations are available to suit your application.
High Precision Touch Switch MT Series
The MT series is the top-of-the-line model of touch switches with a repeatability of 0.5μm, developed jointly with Toyota Motor Corporation.
Many applications in detection mechanisms for minute changes and thermal mutations.